One of the most complex and vital tasks facing the Department of Defense (DoD) is managing its supply chain to effectively and efficiently provide spare parts, equipment, food and other critical supplies in support of U.S. military forces. The DoD’s goal and challenge is to deliver the right items to the right place at the right time – and the right cost – yet it still struggles with achieving Total Asset Visibility (TAV) .
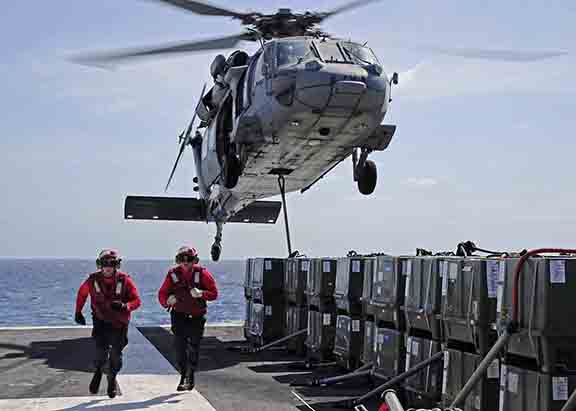
U.S. Navy photo by Mass Communication Specialist 3rd Class Wyatt L. Anthony
By its very nature, the military supply chain is extremely complex and risky. It involves an unstable and unpredictable demand, moving end supply points, and ensuring equipment readiness for war. The DoD is also challenged with fragmentation across its extensive network infrastructures, along with disparate sensor technologies that track the whereabouts and status of its assets.
The U.S. military has made steady progress achieving its TAV goals with advances in automatic information technology, including implementing Radio Frequency Identification (RFID) for asset tracking. However, it continues to face interoperability challenges due to “stovepiped” networks and IT systems that were developed independently with differing requirements and data formats. The challenge is providing a unified infrastructure that can effectively capture massive amounts of data – and turning that “Big Data” into actionable insights.
This is what the Internet of Things (IoT) is all about. The IoT is changing lives in the commercial sector, connecting everything from smartphones, smart appliances, smart home thermostats, wearables and much more. The application of the IoT in the manufacturing industry – dubbed the Industrial Internet of Things (IIoT) or Industry 4.0 – leverages intelligent, connected devices to greatly improve operational efficiency, productivity, and profitability across manufacturing plants and supply chains.
With the rapidly evolving IoT market, the DoD is looking to capitalize on civilian successes and lessons-learned to help manage the sheer volume of data produced for both tactical and logistics operations. DoD representatives actively engage with industry leaders and participate in conferences such as RFID Journal Live to keep abreast of the latest advances in RFID and related IoT solutions, including Tapestry’s Enterprise Sensor Integration (ESI) technology.
Leveraging ESI’s Commercial Successes
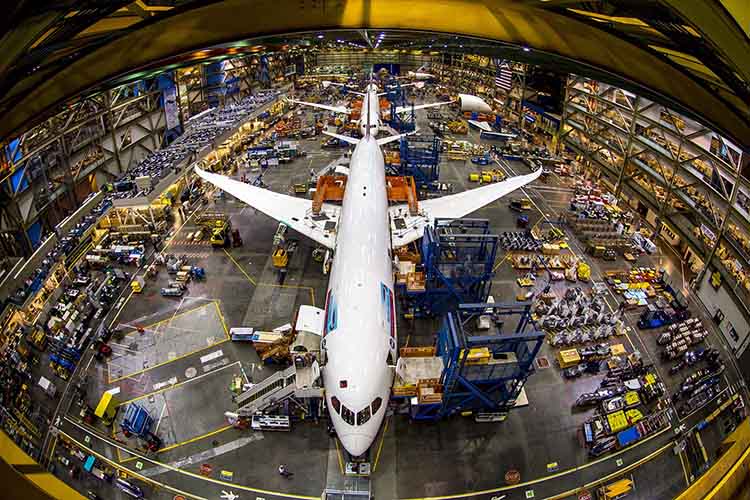
ESI has been deployed across Boeing, including the massive Everett plant, pictured here.
With its proven success in the commercial industry, ESI holds great potential for asset/tool tracking, sustainment and supply chain management for the defense sector. In the commercial aerospace & defense market, ESI has significantly enhanced asset visibility, increased production rates and reduced costs for Boeing and BAE Systems.
At Boeing, ESI has interconnected nearly every aspect of the organization’s asset management and supply chain across 27 major manufacturing sites comprising over 300 buildings. This unity of information, powered by sensor integration, has saved Boeing more than $100 million in the first year alone. The technology, proven to handle up to 6-10 billion RFID tag reads each week, continues to save Boeing millions each year. Today, ESI saves the company an estimated $80 million in recurring annual savings through reduced labor costs, increased workflow efficiency, asset loss prevention, and improved decision-making based on the Big Data analytics.
BAE Systems also rolled out an award-winning ESI-enabled RFID solution last year at several manufacturing sites, including its Electronic Warfare Integrated Manufacturing Center (EW-IMC) in Nashua, NH. Because of its successful implementation, BAE Systems recently captured an award for “Best Manufacturing RFID Implementation” at the 17th annual RFID Journal LIVE conference.
BAE Systems’ primary task was to replace existing manual processes with RFID to effectively track and manage inventory, assets/tools and work-in-process (WIP). The RFID technology, driven by ESI, has automated the tracking of more than 200,000 assets, 30,000 parts and about 6,500 work orders at its plants. BAE Systems reported that it saved 2,400 hours tracking WIP, and an additional 1,248 hours in searching for missing items.
ABOUT ESI
As an IoT middleware solution, ESI integrates disparate sensor technologies to connect people data and processes across factories and supply chains. ESI solves connectivity challenges caused by the proliferation of proprietary IoT devices and tracking solutions that cannot share data with other sensors or networks.
ESI features a unique “sensor-agnostic” platform that ensures interoperability with various hardware and software vendors’ IoT solutions, regardless of brand or data formats. ESI connects sensors ranging from RFID position-information tags, passive and active GPS-enabled WiFi tags to embedded hardware and complex ERP systems, both legacy and next generation technologies. ESI also includes real-time alerts and integration with sensors that monitor temperature sensors, pressure and humidity.
The software platform can be implemented across a global enterprise, either in the cloud or on dedicated servers. With ESI, decision makers have total asset visibility of equipment, tools, cargo and processes – anywhere at any time for 360° supply chain clarity.
As a successfully deployed IoT platform, ESI can help military forces increase efficiencies, reduce costs and enhance situational awareness across its supply chain networks. For more details, download White Paper or watch video below.
About Tapestry Solutions
Tapestry Solutions, Inc. is a global provider of information management software and services for defense, government and commercial markets. We provide mission planning, training and simulation support to maximize readiness for our warfighters. We also help solve logistics challenges for the world’s largest and most complex supply chains. Supporting customers from more than 50 locations worldwide, Tapestry Solutions is part of Boeing Global Services.
Operating as one of Boeing’s three business units, Global Services is headquartered in the Dallas area. For more information, visit www.boeing.com/services.
Contact:
Janet Dayton
Boeing Global Services
janet.l.dayton@boeing.com
The appearance of U.S. DoD visual information does not imply or constitute DoD endorsement.